2025 Author: Leah Sherlock | [email protected]. Last modified: 2025-01-24 17:46
The famous Ipatiev Chronicle tells us the story of the marvelous creations of Russian master jewelers who decorated their products with enamel - a composition of colored vitreous powder hardened after firing, which made it possible to achieve an extraordinary visual effect. This technology came to Russia from Byzantium, where it appeared in the 6th century. Nowadays, the ancient word enamel has gone out of circulation, giving way to the now used term - artistic enamel.
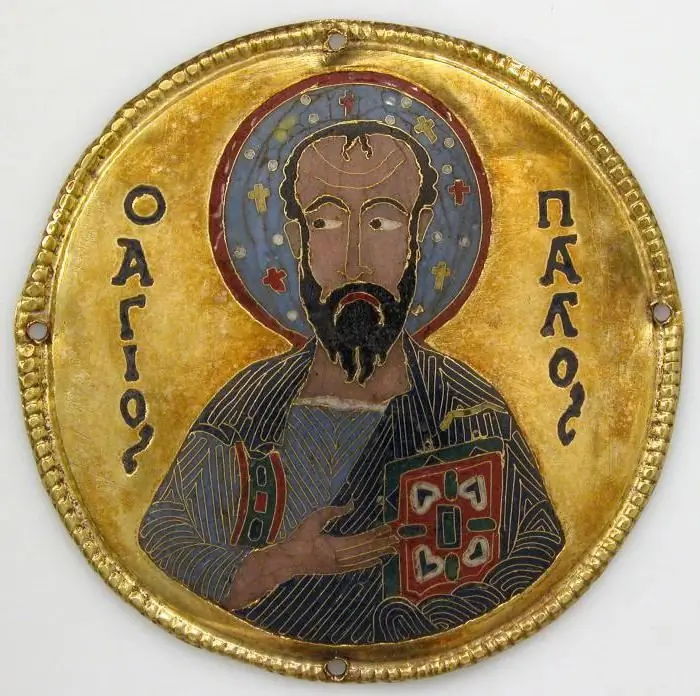
What is decorative enamel?
Before starting a conversation about what constitutes an artistic technique called "cloisonne enamel", let's dwell on the description of this very composition used by jewelers and craftsmen. As mentioned above, enamel is a powder obtained by grinding colored vitreous plates.
Moistened with water and turned into a continuous pliable mass, the composition is applied to the cells made on the surface of the product. The next step in the process is roasting. It is produced either in a kiln orspecial gas or gasoline burner. Under the action of high temperature (from 700 to 900 ° C), the vitreous mass hardens and takes on its unique appearance.
Features of working with enamel
Depending on the composition of the crushed vitreous mass, temperature, and the duration of firing, the resulting enamel may have a different degree of transparency or be completely opaque - deaf. This opens up wide creative possibilities for the master, as it allows you to achieve a wide variety of effects.
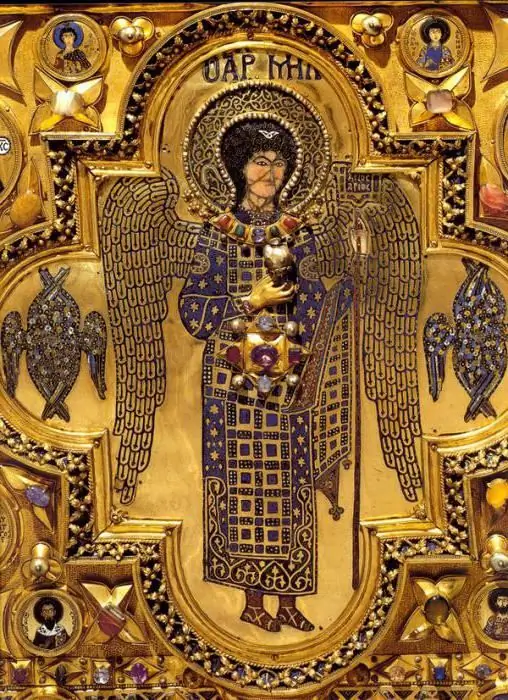
The range of techniques used in this kind of work is very rich, and one of them is cloisonné enamel. Jewelry made with its use is not widely used and is considered elite. The reason lies in the complexity of their manufacture and the impossibility of mechanizing the production process. Each item is a unique work of art. If we also take into account that noble metals are often used in the work, then their high price and low availability become clear.
How cloisonne is made
First of all, on the gold, silver or cupronickel (rarely copper or steel) surface, which is the basis of the composition, the contour of the future drawing is engraved, and sometimes cut through. Then metal partitions are soldered along its edges, the thickness of which rarely exceeds one millimeter. These partitions, which gave the name to the described type of enamel technique, form both closed and open cells, whichare filled with another liquid and viscous multicolored mass.
After the enamel hardens during the firing process, the product is ground and polished. This is done in such a way that the surface of the partitions and enamel creates a single plane. The technique of cloisonné enamel is much more complicated in that during firing, the material layer shrinks and becomes lower than the septum. As a result, it is necessary to replenish the cells and re-fire the product. Depending on a number of technical factors and the artistic intent of the author, firing can be repeated from five to one hundred times.

Unique products and consumer goods
It should be noted that the impossibility of influencing the processes occurring in enamel when exposed to high temperatures determines the originality and uniqueness of each product. It is almost impossible to achieve the same effect twice, so each piece made using this technique is unique.
Cloisonne enamel is not the only enamel technique in arts and crafts. Along with it, the so-called excavation is also widely used. It differs from the partition wall in that it is not the cells formed by soldered partitions that are filled with a vitreous composition, but specially made recesses, the shape of which corresponds to the lines of the pattern. In modern jewelry production, stamped or cast blanks are usually used for this purpose. In the same industry, imitation of cloisonné enamel is also used in the manufacture of consumer goods.
Stained glass window effect
Cloisonne enamel has one more variety. It is called stained glass or window enamel. This technique is characterized by the fact that it does not use a metal base. It got its name due to the fact that the products made on its basis resemble stained-glass windows in appearance. They are completely transparent, and the light, penetrating through the vitreous mass, creates the illusion of colored stained glass framed by metal.
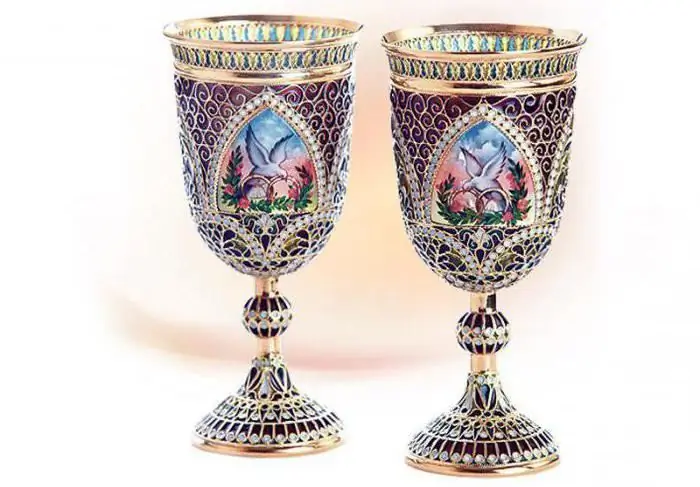
Products made using this technique are extraordinarily beautiful. The metal frame filled with enamel looks like fine lace made of gold, silver or copper. It is made by sawing or mounting and subsequent soldering of parts made of wire twisted in a special way. Colored enamel filling the gaps between the partitions creates an indescribable play of light.
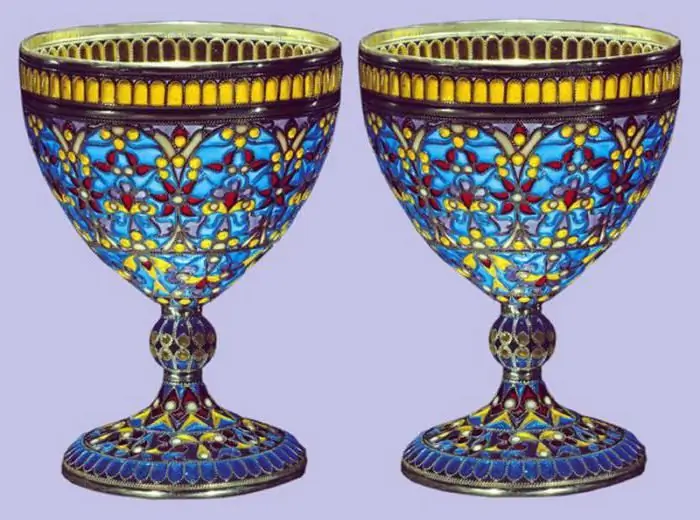
Chinese enamel tradition
Chinese enamel occupies a special place in the history of arts and crafts. Cloisonne enamel, called clausane, was not an invention of the Chinese themselves, but came to them from France, but received a peculiar development, due to local national traditions. From its original source, it inherited mainly the name, which comes from the distorted French word Cloison - "partition". Before this type of enamel technique appeared in China, its excavation version was used there.
In the Beijing Palace Museum in a wide varietyworks of arts and crafts are exhibited, among which Chinese enamel stands out. Cloisonne enamel is represented mainly by Xuande and Jingtai period wares from the 15th century. This is no coincidence, since the period of the Ming Dynasty, to which the mentioned rulers belonged, is considered the time of the greatest flowering of this area of art. Based on their own technologies, as well as those borrowed from Europe, Chinese craftsmen decorated table and floor vases, cups, candy bowls, and various lamps with extraordinary imagination.
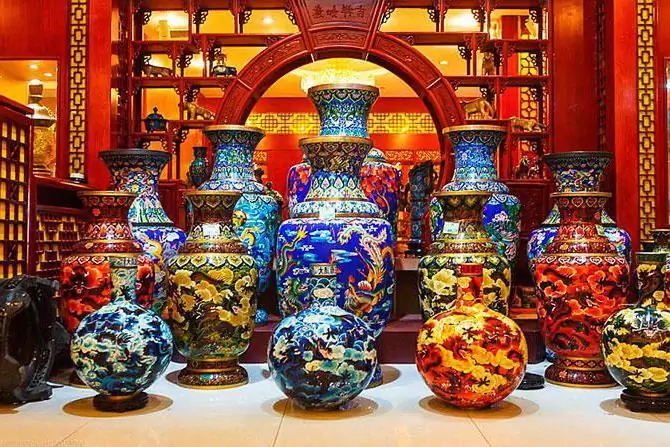
Artistic enamel from Georgia
Georgian cloisonné enamel is also highly respected by collectors and just art lovers. Its earliest known samples date back to the 9th century, and they were made using the same technology that is used today. The art of Georgia, which is distinguished by its original color and inexhaustible energy, has embodied many European and Eastern traditions. That is why cloisonne enamel, the technology of which came to these parts from Western Europe, so organically fit into it. Here it was not only mastered, but also further developed, thanks to which many masterpieces of the national Georgian school appeared.
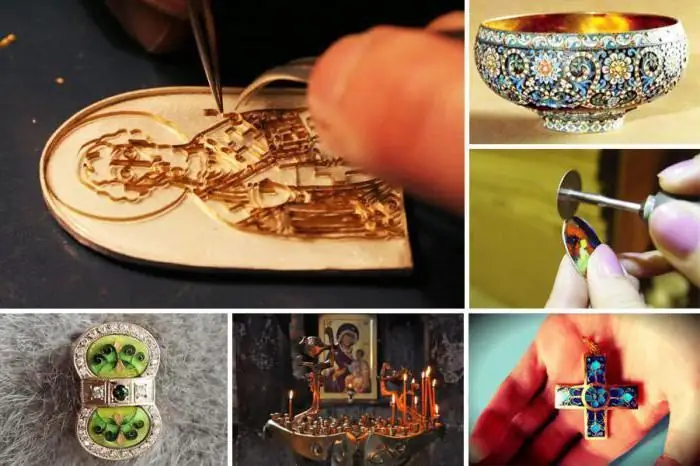
Enamel in past times and today
It is known that masters of cloisonne enamel of past centuries used other components than their modern followers to obtain the composition they needed. ATone of the old recipes says that the preparation of enamel requires one part of pure quartz sand, one part of boric acid and two parts of red lead. To give the composition the desired color, various pigments were used in the form of oxides of cadmium, cob alt or copper.
In the 20th century, enamel technique went beyond its traditional use and, in addition to arts and crafts, began to be used wherever a durable and chemically resistant surface is required. Technical enamels appeared. Accordingly, the technology of their preparation has also changed.
Cloisonne enamel: master class
At the end of the article, we give a detailed story on how to make a panel yourself, made using the technique of partition enamel. This kind of master class will allow everyone to try their hand at creating a work of arts and crafts.
First of all, you need to take a copper plate of suitable size and thickness and anneal it until it turns red, and then cool it in water. This will give the material softness and protect it from deformation during further firing of the enamel itself. After that, the plate is wiped and carefully cleaned with sandpaper. A perfectly smooth surface should not be achieved, as a slight roughness will contribute to a better connection of the metal with the enamel.
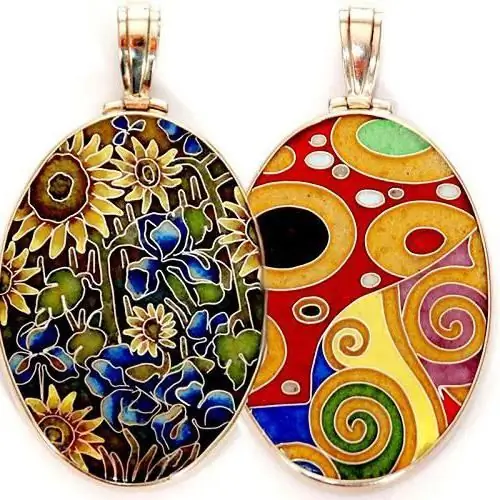
From drawing to installation of partitions
The next step is drawing a pattern on the plate. It can be either your own composition or transferred frombooks using tracing paper and carbon paper. To make the image clearer, the plate can be pre-coated with white gouache. When the drawing is marked, it should be scratched with a steel scriber used in plumbing. After that, the plate is thoroughly washed and ignited again on fire.
For the manufacture of partitions, it is recommended to use copper wire with a diameter of approximately 0.8 mm. It is first passed through rollers or simply flattened with a hammer. The resulting strip is glued with an edge to the plate, exactly repeating the line of the drawing. For this work, alcohol glue BF-6 is usually used.
Enameling and firing
For the manufacture of panels, enamel should be used in the form of a powder mass. On sale there are its varieties with the addition of gold or silver particles, which gives the product a more expensive and sophisticated look. The powder is diluted with water and the resulting mass fills the gaps between the partitions. For this purpose, it is convenient to use a spatula and a brush. It is important that the enamel layer is evenly laid evenly along the height of the partitions.
The next step will require a drying oven. In it, the product is dried at a temperature of 60 ° C until the water completely evaporates from the enamel mixture. Upon completion of this process, the plate on a stand made of heat-resistant steel is placed in a muffle furnace and fired. If it is possible to regulate the temperature in the furnace, then it is desirable to bring it up to 850 ° C, if not, then heating should be continued until the surface of the product becomesglossy.
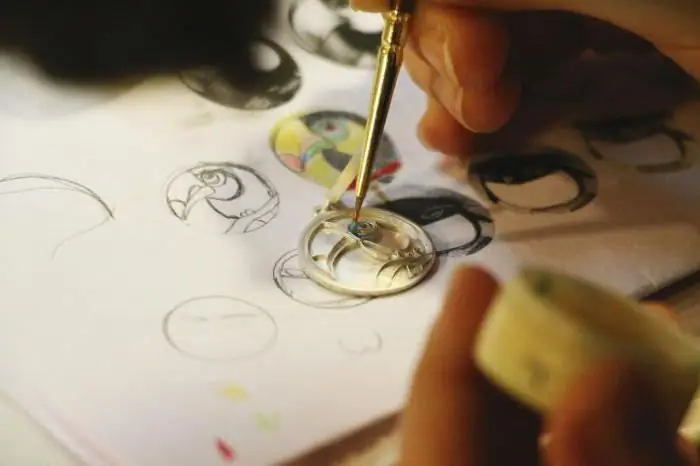
Final stage of work
After making sure that the firing is completed, the plate is taken out of the oven with long tongs and placed on a metal surface, pressed from above with a flat and even load, the weight of which should be at least ten kilograms. In this form, the product cools down. Then the load is removed and the needle file is used to clean up irregularities and remove scale.
Cloisonne enamel is not an easy technique, and the first time the artistic qualities of the product may turn out to be unsatisfactory. In this case, you can add the required amount of enamel to the cells and repeat the firing, but this can be done no more than four times, since this type of enamel becomes discolored with a larger amount.
Recommended:
Glass painting: types, techniques, master class for beginners
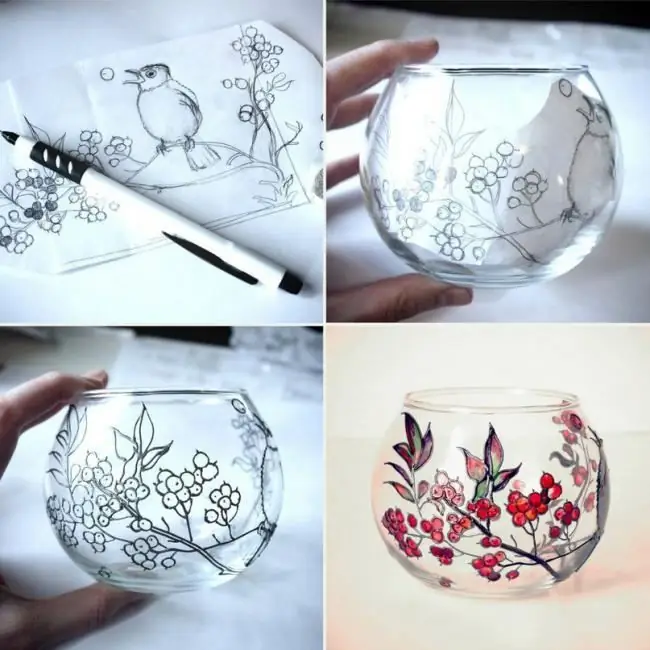
Glass painting is a type of art with a long history. Once its secrets were known only to masters. Over the past century, there has been a significant leap in paint technology. Today, glass painting can be done not only by an artist, but also by a person who is far from arts and crafts
How to use gouache in drawing: a master class on working with paint
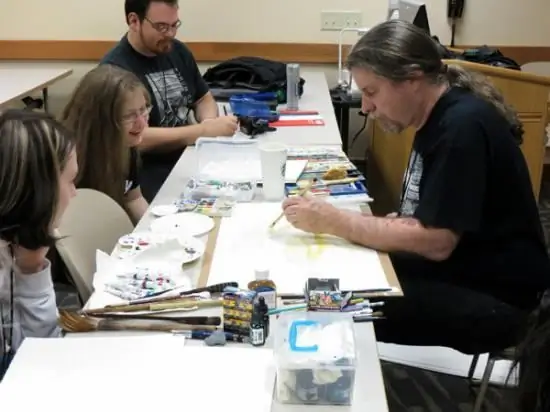
The topic of our article is gouache. We will begin the master class on working with it with a description of the properties of the paint. It is available in two versions: poster, which is most often used at school in drawing lessons, and art - for professional work
Flageolet - what kind of musical technique is this? Definition, technique of playing the harmonic on the guitar

What is a harmonic, how to take it on the guitar, when did it appear? You can find answers to these and other questions in this article, as well as find out in what styles harmonics can and should be played. And, of course, perhaps the most important thing - you will learn how to perform them in your works
Glazing - what is it? Application technique, master class
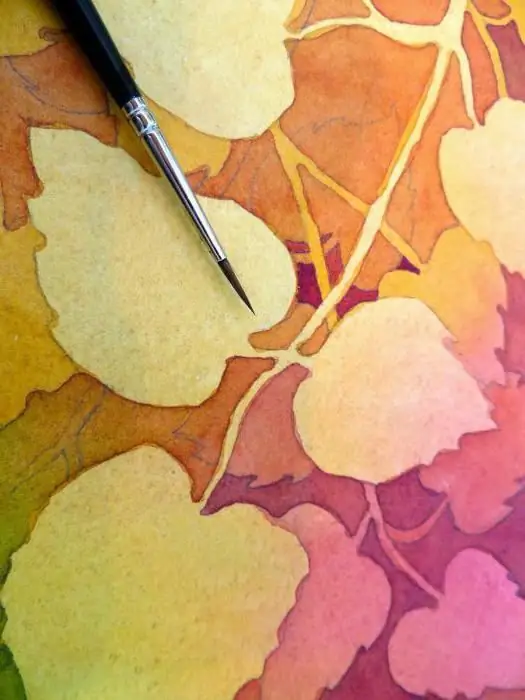
Do you want to learn a new painting technique called glazing? This is the application of transparent layers of paint to a base in order to obtain beautiful shades or unusual effects in a painting or decorative object
Why didn't the Master deserve the light? The image of the Master in the novel by Mikhail Afanasyevich Bulgakov "The Master and Margarita"
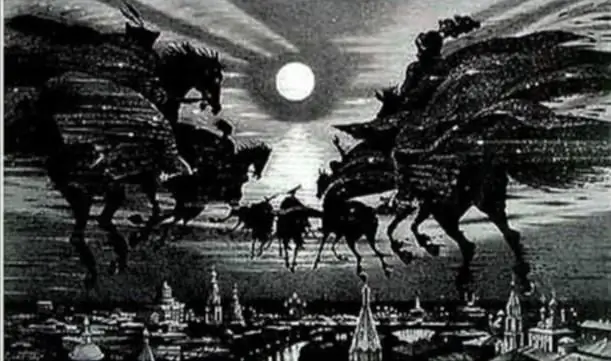
The relationship between Yeshua Ga-Notsri and Woland in M. A. Bulgakov's novel "The Master and Margarita" is a very interesting topic, which at first causes bewilderment. Let's look into these intricacies and relationships between the Kingdom of Heaven and the underworld